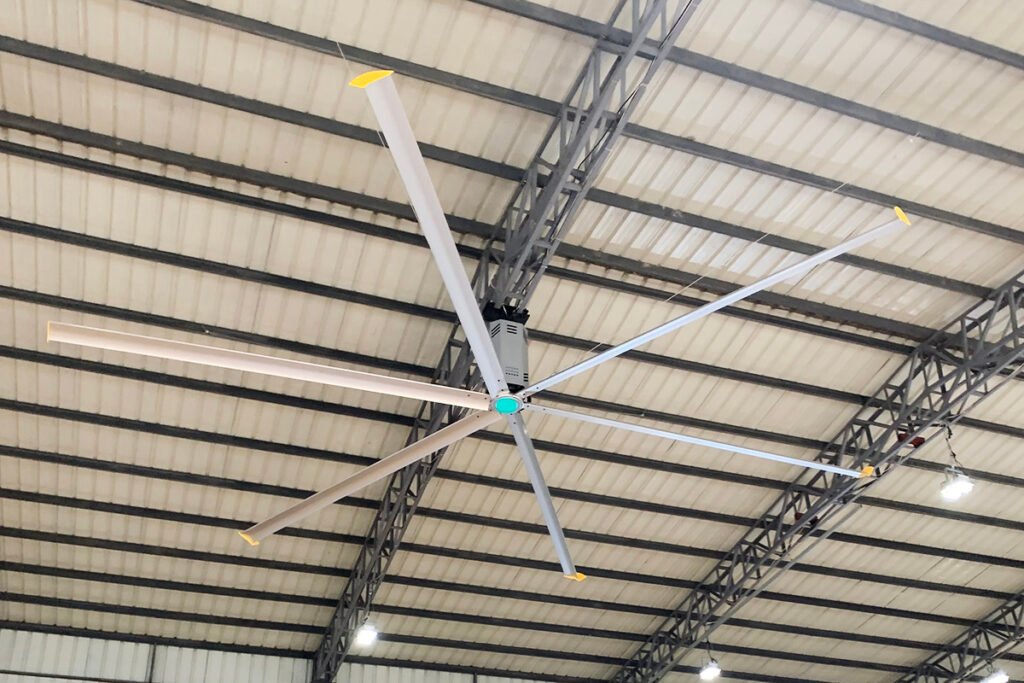
The optimization of High Volume, Low Speed (HVLS) industrial fans in fluid dynamics is a complex process that involves multiple aspects of consideration and design improvement. Here is a detailed introduction to the fluid dynamics optimization of HVLS industrial fans:
- Blade Design Optimization: The blade design of HVLS fans is a key factor affecting their fluid dynamic performance. By optimizing the shape, size, and angles of the blades, the airflow efficiency and thrust of the fan can be improved. Aerodynamic performance analysis of the blades usually involves Computational Fluid Dynamics (CFD) simulations to predict the flow field distribution and pressure changes under different conditions.
- Flow Field Simulation and Analysis: Utilizing CFD software for flow field simulation allows for the prediction of fan performance, including air distribution, velocity fields, and pressure fields, during the design phase. By analyzing this data, designers can adjust the fan’s blade layout, blade curvature, and blade clearance to achieve optimal aerodynamic performance.
- Reducing Blade Clearance: The blade clearance significantly affects the aerodynamic performance of the fan. Larger clearances can lead to air leakage, reducing the efficiency of the fan. By reducing blade clearance, leakage losses can be minimized, and the aerodynamic efficiency of the fan can be improved. However, optimization of clearance needs to consider mechanical strength and ease of maintenance.
- Fluid-Structure Interaction (FSI) Dynamic Assessment: The structure of HVLS fans is dynamically affected by the airflow during operation. Through FSI dynamic assessment, the vibration and deformation of the fan blades under the influence of airflow can be analyzed, thereby optimizing the structural design and enhancing the stability and durability of the fan.
- Noise Control: The noise generated by fans during operation is a concern in industrial applications. By identifying the main sources of noise, such as blade passing frequency (BPF) and its harmonics, through CFD simulations and acoustic analysis, blade design and fan layout can be optimized to effectively reduce noise levels and improve the working environment.
- Fan Layout and Installation: The layout and installation position of the fan have a direct impact on the air distribution and efficiency. A rational layout can ensure uniform airflow coverage over the required area, avoiding dead spots and vortex generation. Additionally, the installation height and angle of the fan need to be optimized based on the spatial structure and airflow requirements.
- Materials and Manufacturing Processes: The materials and manufacturing processes of fan blades also affect their fluid dynamic performance. Lightweight and high-strength materials can reduce the inertia of the blades, improving response speed. At the same time, precise manufacturing processes can ensure the accuracy of blade shapes, reducing the impact of manufacturing errors on performance.
- Performance Testing and Validation: It is essential to evaluate the actual performance of the fan through experimental testing during the design and optimization process. Through wind tunnel tests, noise tests, and efficiency tests, the actual performance of the fan can be assessed, and further optimizations can be made based on test results.
By implementing the above measures, the fluid dynamic performance of HVLS industrial fans can be significantly enhanced, leading to higher airflow efficiency, lower energy consumption, and an improved working environment. These optimizations not only improve the performance of the fan but also extend its service life and reduce operating costs.